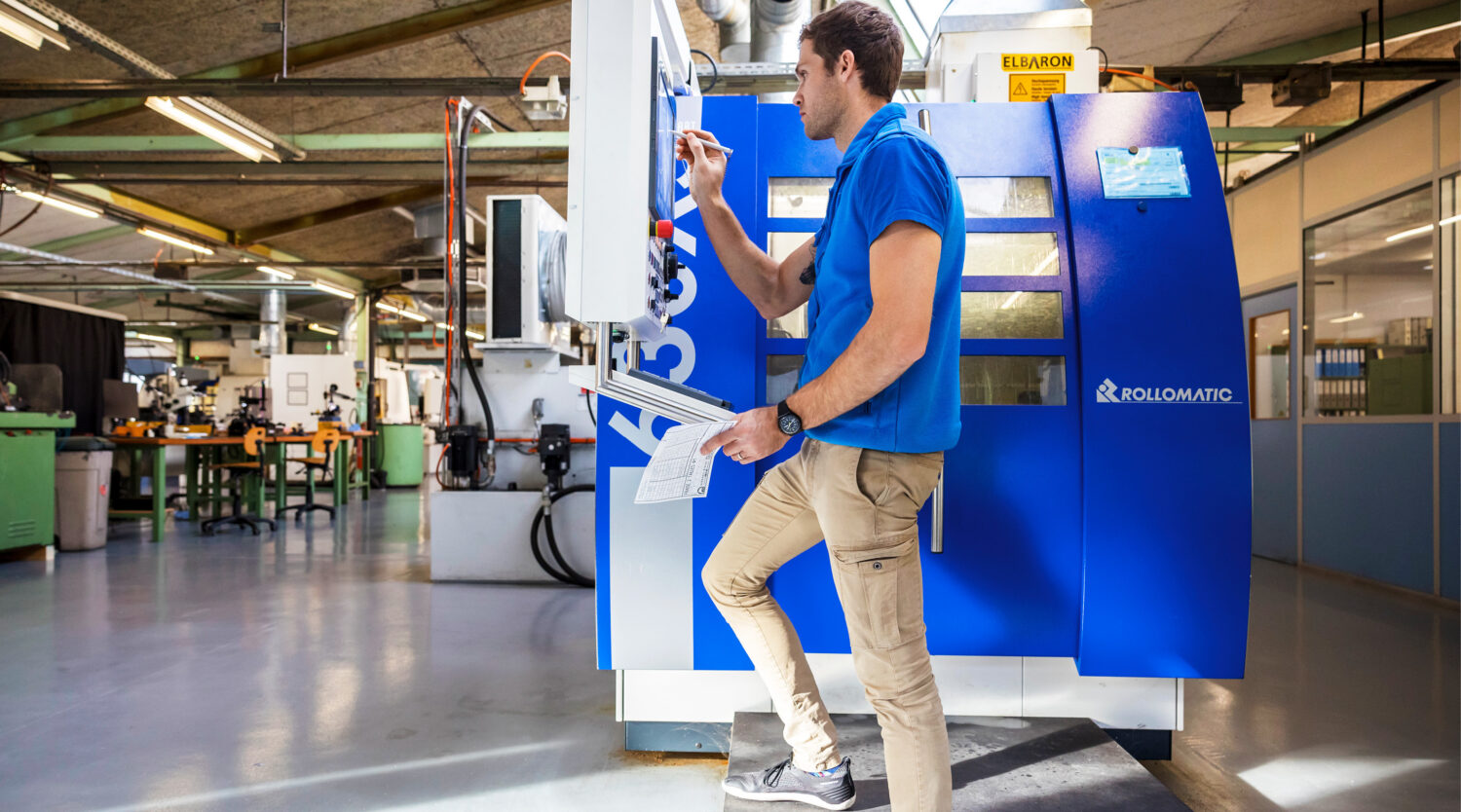
A traditional SME develops the tools of tomorrow
For over 100 years, Eskenazi SA, based in Carouge near Geneva, has been manufacturing cutting tools for precision mechanics, primarily for the watchmaking and medical industries. This family business with its 35 employees can look back on a long company history, but is investing in the future with its own research and development department.
Among other things, the SME is working together with universities to further develop and improve its tools. “The research projects enable us to find new machining techniques and to develop the tools of tomorrow,” says Gilbert Grosjean, who is both Head of Production and Head of R&D.
One such “tool of tomorrow” is the micro-cutting tool with internal cooling that Eskenazi has developed together with the Haute école du paysage, d’ingénierie et d’architecture de Genève (HEPIA): instead of the lubricant needed for milling being supplied from outside, it comes directly from tiny holes in the tool itself.
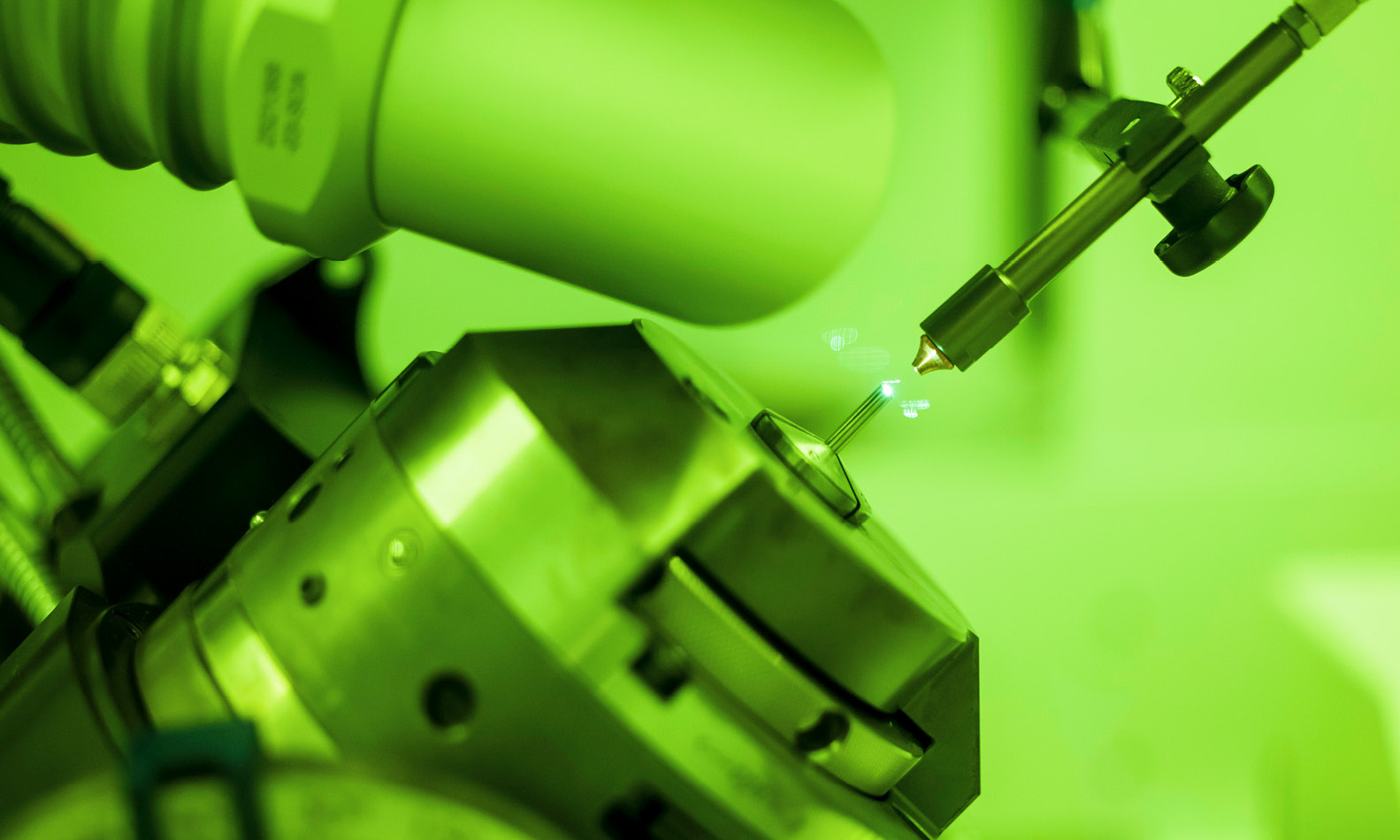
More precise and efficient milling
High temperatures are generated during the machining of metals. A cooling lubricant, usually oil-based, reduces the friction between the tool and the workpiece, cools the entire system, and carries away the resulting chips.
Since the coolant now comes directly from the cutting tool itself, it gets closer to the cutting surface. Work can be done more precisely and quickly, and wear is reduced. “Cooling through the tool tip results in a significant improvement in terms of the micro-cutting tool’s service life and performance,” says Walter Gilli, R&D engineer at Eskenazi. Until now, internal cooling of this kind was only possible for significantly larger tools. A patent application has been filed for this development.
An initial project was completed in 2019, and the innovative tools have been listed in Eskenazi’s catalogue since April 2022. Even if the technology was mature after completion of the project, it always takes a certain amount of time to successfully manufacture a product on an industrial scale, Walter Gilli explains.
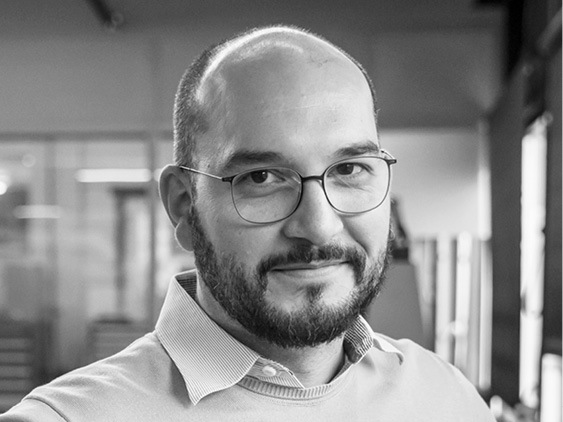
“Without the support of Innosuisse, we would have to rely on trial-and-error for the development. It would take a lot more time, and the result would probably never be as good as it would be through research-based findings.”
Walter Gilli
R&D Engineer at Eskenazi
Further research on a more sustainable process
HEPIA and Eskenazi have been working on the follow-up project since 2022 – once again with the support of Innosuisse: For this purpose, investigations are being carried out to determine whether supercritical carbon dioxide (also known as supercritical CO2, or sCO2 for short) is suitable for cooling during milling.
Supercritical carbon dioxide is a liquid that is compressed at 36 degrees Celsius, and that becomes cold and gaseous without pressure, making it ideal for the machining process, explains Walter Gilli. “While still inside the tool, the lubricant is a liquid; as soon as it exits the tool, it turns into gas.”
The use of sCO2 makes the milling process more ecological, Gilbert Grosjean stresses. There is no longer any need for petroleum-based materials as part of the cooling process, and initial tests have revealed that the entire process also requires less energy. In addition, tool wear when milling materials such as titanium or gold is reduced. And the cut parts will no longer have any oil residue and will be easier to clean. This is especially important in the medical field.
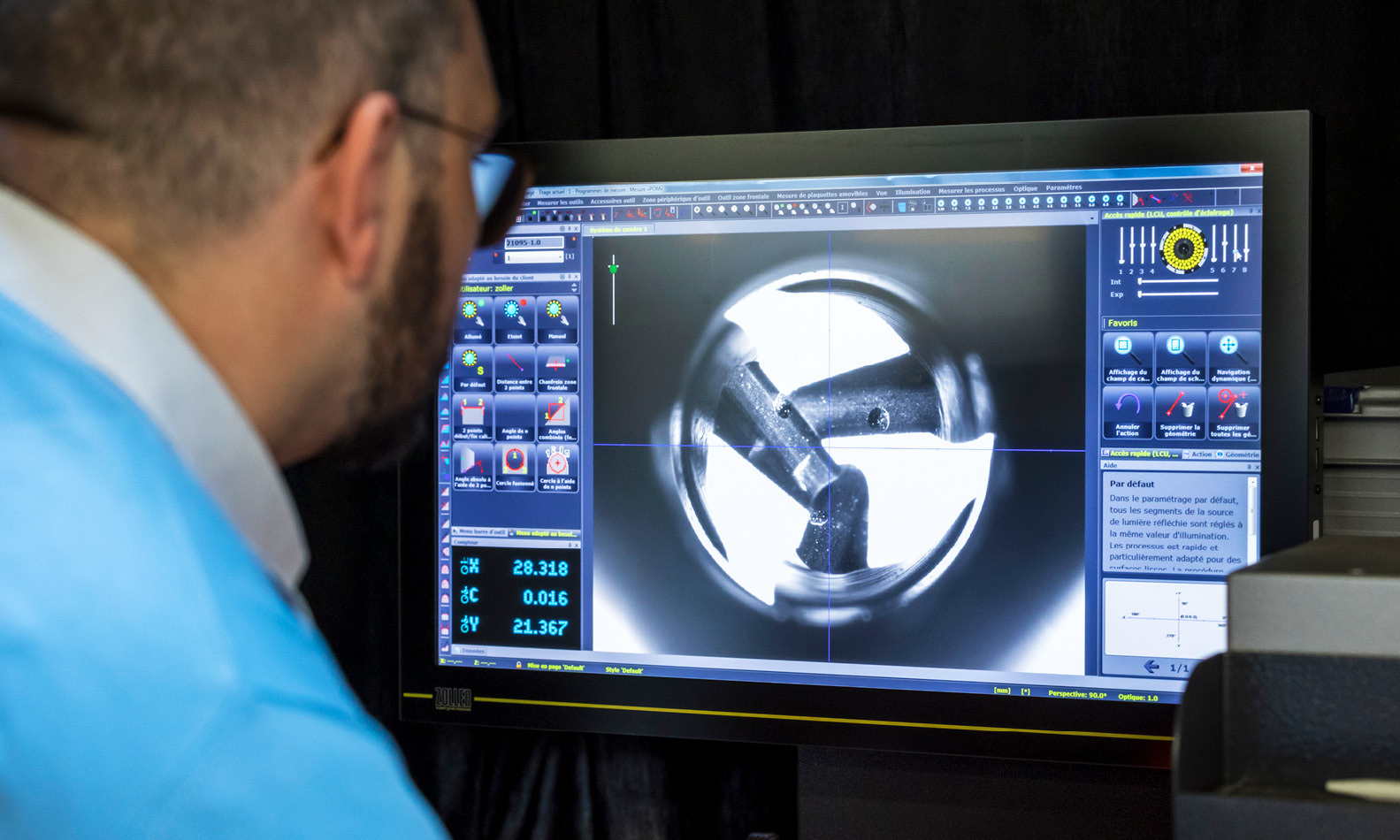
Important collaboration with universities
Eskenazi conducted preliminary tests that demonstrated this technology’s high potential. “From initial tests, we can see that supercritical carbon dioxide behaves better than oil with certain materials,” says Walter Gilli. “The project will now show exactly what happens when the carbon dioxide exits the tool.” With its expertise, HEPIA is the ideal research partner, he says. “The collaboration helps us to definitively understand the interrelationships involved here. And only in this way can we develop a reliable product.”
While HEPIA has been busy during the first months of the project, researching the dynamics of the change from liquid to gas and its effect in the milling process, Eskenazi’s R&D department has been conducting tests and trying to determine which tools are best suited for use with sCO2.
“We are confident that the project goals will be achieved and that something usable will emerge,” says Walter Gilli. We will develop a product from it as quickly as possible; our infrastructure is already ready and waiting. We are sure that such a product can be marketed quickly. We have already found interested parties.”
In constant dialogue
As part of another ongoing Innosuisse project, the Geneva-based SME is collaborating with the University of Geneva. This is the ideal partner when it comes to innovative tool coatings, says Gilbert Grosjean. Relationships with various universities and departments, as well as personal exchange with professors and other university employees, are essential for an innovative SME in a niche market, emphasises Eskenazi’s Head of R&D. “Through constant dialogue, we know who is working on what, and we can develop ideas and solutions together.”
And sometimes the transfer of knowledge between research and companies also leads to the recruitment of personnel: Walter Gilli was still working as an assistant at HEPIA during the first project – and moved to Eskenazi as an R&D engineer after the project was completed in 2019.
Support from Innosuisse
- 1 innovation project with HEPIA
- 1 innovation project with the University of Geneva
- 1 CTI innovation project
- Innovation cheque
- Mentoring